Nutsche Filter Dryer for Crystallized Cannabidiol (CBD) Isolate Slurries
Introduction
For many years, the CBD industry fought archaic regulations and a lack of mass acceptance by consumers. This has all but changed recently thanks to improved legislation and a better understanding of the medicinal benefits.
This new resurgence has resulted in CBD isolate manufacturers facing the challenge of scaling their manufacturing capacity while ensuring consistent product cost and quality, workplace safety, and meeting regulations.
These manufacturing challenges can be met with technology that follow Current Good Manufacturing Practices (CGMPs) and Clean in Place (CIP) methodologies.
In the filtration process of making CBD Isolate, typically a vacuum Büchner funnel is utilized to pull the solvent and cannabinoid mixture through the filter – leaving behind the crystalline CBD. The crystalline CBD is then dried in a separate, stationary tray dryer. However, this process is inefficient to scale-up, resulting in production bottlenecks and safety concerns.
The ZWAG filter, an all-in-one Agitated Nutsche filter dryer offers manufacturers the ability to scale their production goals while maintaining CGMP compliance and full solvent containment. At the largest size, the ZWAG filter is able to crystallize, filter, wash and dry over 2,000kg of dry CBD isolate per batch with zero detectable residual solvent.
Background
Cannabidiol (CBD) is a naturally occurring cannabinoid that has been cultivated to grow in high concentrations in hemp plants. In recent years this compound has shown preliminary evidence as a useful treatment in many ailments and continues to grow in usage.
While CBD comes in various forms that can contain other cannabinoids, terpenes, and THC, its purest form is CBD Isolate. During the isolate production process, the CBD extract is refined to strip away all impurities and photocannabinoids, including THC, resulting in a final product that is a 99% pure, odorless, and tasteless crystalline powder. This powder is easily able to be mixed with oils, supplements, gums, and extracts with a high degree of dosage and purity certainty. Additionally, this isolate can be used as a building block to synthesize other minor cannabinoids.
Production of CBD Isolate
To produce CBD isolate, CBD must first be extracted from the hemp. This follows well-known crude CBD extraction processes. Post extraction the CBD concentrate is still full of plant material so further purification is required (Figure 1 Stage 1). First a filtration & winterization stage removes fats, lipids, proteins, and residual biomass from a chilled mixture (Figure 1 Stage 2).
After winterization, the CBD oil is further purified using a fractional distillation that helps recover extraction and/or winterization solvent while also removing other undesirable compounds such as chlorophyll and terpenes. The product of distillation is a clear, refined oil containing CBD and other minor cannabinoids (Figure 1 Stage 3).
The crystallization and isolation processes are used to further separate CBD from other minor cannabinoids. To begin crystallization, the CBD oil is dissolved in a non-polar solvent in a reactor. Typically, pentane is the non-polar solvent of choice, but other examples include hexane or heptane. The temperature of this solution is gradually cooled until precipitation begins to occur. Temperature and agitation speed are both reduced until the solution is fully crystallized (Figure 1 Stage 4).
In the final stage of producing a pure CBD isolate, the slurry containing CBD crystals must be filtered, washed, and dried (Figure 1 Stage 5). The filtration stage separates the CBD crystals from the mother liquor. The crystals should be washed with ice cold non-polar pentane, to remove impurities contained in the mother liquor from the surface of the isolate. The isolate is soluble in pentane so care should be taken that the use of wash liquor is minimized to prevent isolate loss. Finally, all residual pentane is dried from the crystals down to PPM levels prior to downstream packaging.
Agitated Nutsche Filter Dryers: The All-In-One Solution
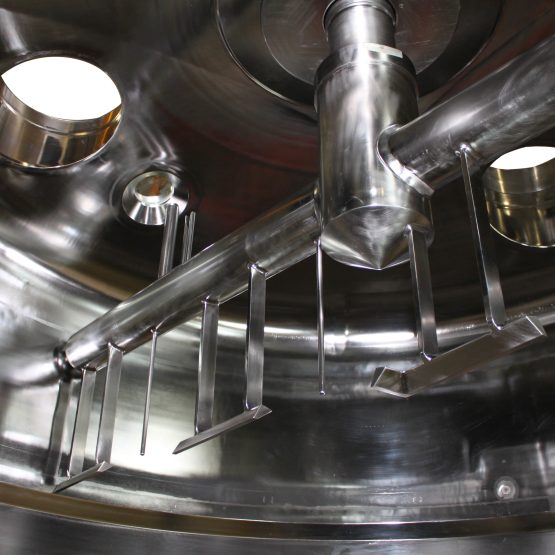
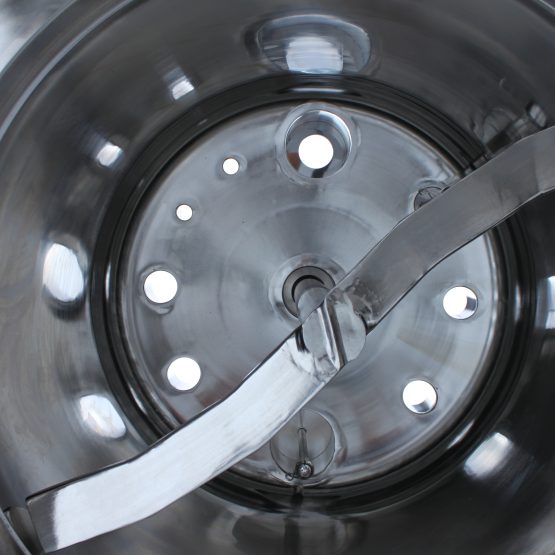
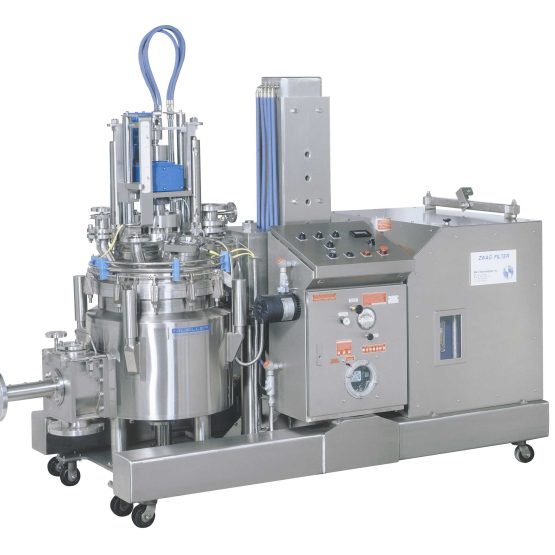
Anatomy of the Agitated Nutsche Filter Dryer
The Steri Technologies ZWAG Filter features a single filter plate located at the bottom of a jacketed pressure vessel. The single plate allows build-up of a large amount of cake that is beneficial for slurries containing up to 70% suspended solids.
During filtration, the slurry is forced downwards through the filter plate by external nitrogen pressure. The solids collect on the top of the filter plate while the filtrate passes through and exits through a nozzle centered under the filter plate. Operating under a nitrogen blanket ensures safe production and eliminates fire risk in the presence of flammable solvents.
The ZWAG features an agitator that is used to continuously smooth and evenly distribute the cake. Often, thick cake buildup has a tendency to crack. When this occurs, slurry and wash liquids will take the path of least resistance which can lead to poor filtration and washing performance. The smoothening action of the ZWAG ensures an efficient and consistent wash each and every time.
Once the filtration is complete, the mother liquor can be displaced from the cake using a cold solvent wash. Good temperature management is critical during this process to reduce CBD product loss. The ZWAG features a jacketed agitator and vessel, which helps maintain the temperature required for the solvent wash.
The ZWAG offers the ability to vacuum dry as well to remove all residual solvents. Vacuum reduces the boiling point of the residual solvent below ambient temperatures. The same agitator and vessel jacket can also be heated to improve drying times. The agitator is additionally used to turn over the solids improving drying efficiency and overall cake moisture content.
Once a bone-dry isolate is achieved, the side discharge valve can be opened for removal of all solids from the filter without breaking containment. The CBD isolate is fully contained and is not exposed to outside contamination sources ensuring product integrity, nor are operators exposed to potential hazards.
If required, a CIP cycle can be implemented on the filter using CIP nozzles or flooding to ensure batch to batch integrity.
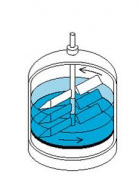
Uniformity for Quick Filtering Products
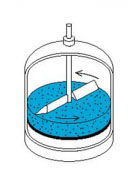
Smoothing for Quality
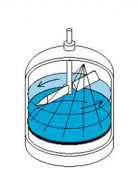
Washing for Purity
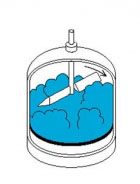
Efficient & Complete Drying
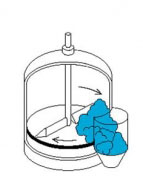
Contactless & Contained Discharge
Advantages of the ZWAG® for CBD Isolate Production
All-In-One Operation with Ultimate Control
The ZWAG® filter has every tool needed for the ultimate batch control: Pressure and vacuum rated, agitation, replaceable filter media, temperature measurement and control, and contained discharge. Everything necessary to filter, wash, and dry CBD isolate combined in one simple piece of equipment.
Isolate Drying to Undetectable Levels of Residual Solvent
Through the use of the agitator, the ZWAG® filter has the ability to dry isolate to undetectable levels of residual solvent. The agitator mixes and turns over the cake while under vacuum and an elevated temperature ensuring that all residual solvent is evaporated. This ensures that zero solvent is left behind in the drying process leaving you with a pure, contaminate free CBD isolate.
Safety Through Containment
Through all operation stages, the process is fully contained, a critical element when handling hazardous solvents in large volumes. The vessel can be kept inert through nitrogen blanketing, preventing solvent vapors from being able to escape from the filter. Additionally, no contact is made with the final product keeping operators safe and product pure; guaranteed.
Proven CGMP Design
ZWAG® Filters have been used for decades for production of Active Pharmaceutical Ingredients. These compounds can be highly toxic requiring superior containment capabilities that the ZWAG accommodates through sanitary, tri-clamp connections and cleaning in place (CIP) spray balls. As CBD production trends towards pharmaceutical style regulation, trust the equipment that has already been industry tested and proven.
Sized to Meet Exact Process Requirements
Agitated Nutsche Filter Dryers come in a wide range of sizes ranging from 0.1m2 to 6m2 in surface area and 50L – 6000L. At the largest size, ZWAG units are able to process over 2,000kg of dry CBD isolate per batch.